Chiller vs. VRF Systems: Comparative Analysis
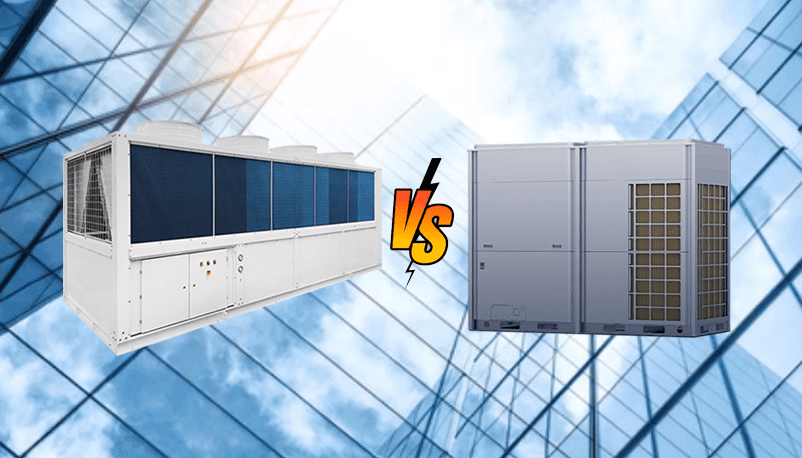
Chiller vs. VRF Systems: Comparative Analysis
Selecting the appropriate air conditioning system for commercial or large-scale applications often involves choosing between centralized chiller systems and Variable Refrigerant Flow (VRF) systems. This article compares water-cooled chiller systems and air-cooled VRF systems across key parameters including cost, installation, and maintenance considerations.
A common industry guideline suggests that chiller systems may become more advantageous than VRF systems when the total cooling load exceeds approximately 1000 refrigeration tons (RT). While VRF systems typically have lower initial capital costs, their operating costs can be higher, potentially making chillers a more economically viable long-term solution for very large capacity requirements due to higher operational efficiency.
VRF systems are recognized for energy efficiency, especially under part-load conditions, and offer significant flexibility in capacity modulation and installation configuration. However, large-scale buildings often utilize chiller technology for primary cooling loads for reasons related to efficiency at scale, maintenance, and system simplicity.
Cost Comparison
(Note: The following cost examples are illustrative and based on estimates for a project in Asia, converted from MYR to USD at an approximate rate of 1 USD = 4.7 MYR. Actual costs vary significantly based on location, specific equipment, labor rates, and project details.)
Capital Cost
Generally, the initial capital cost for a water-cooled chiller system tends to be higher than for an air-cooled VRF system of equivalent capacity.
- Estimate: A water-cooled chiller system might be approximately 10% more expensive per refrigeration ton (RT) than an air-cooled VRF system. For a 1200 RT project, the water-cooled chiller system could be about $128,000 USD more expensive initially than the air-cooled VRF system based on these estimates.
Estimated Capital Cost of a 1200 RT Project (Illustrative, USD)
Cost Component | Water-Cooled Chiller System | Air-Cooled VRF System |
---|---|---|
Preliminary | $21,300.00 | $21,300.00 |
Equipment | $1,223,000.00 | $1,096,000.00 |
Commissioning | $10,600.00 | $10,600.00 |
DLP Service | $21,300.00 | $21,300.00 |
Total Capital Cost | $1,276,200.00 | $1,149,200.00 |
Operating Cost
Water-cooled chiller systems typically exhibit higher energy efficiency, leading to lower operating costs compared to air-cooled VRF systems.
- Estimate: The annual operating cost of an air-cooled VRF system might be around 15% higher per RT than a water-cooled chiller system. Using the illustrative 1200 RT building example, the owner might pay approximately $58,500 USD more each year in operating costs with an air-cooled VRF system compared to a water-cooled chiller system.
Estimated Operating Cost of a 1200 RT Project (Illustrative, Annual, USD)
Cost Component | Water-Cooled Chiller System | Air-Cooled VRF System |
---|---|---|
Annual Electricity Cost | $361,700.00 | $417,000.00 |
Annual Water Cost | $12,300.00 | – |
Annual Maintenance | $16,200.00 | $31,700.00 |
Total Operating Cost | $390,200.00 | $448,700.00 |
Return on Investment (ROI)
Despite the higher initial investment, the lower operating costs of water-cooled chiller systems can lead to a relatively short payback period compared to air-cooled VRF systems in large-scale applications. Based on the illustrative example, the ROI period could be around 3 years. However, this calculation is highly project-specific. VRF systems remain advantageous in scenarios where their specific benefits outweigh the lifecycle cost difference.
System Definitions
Chiller Systems
Chillers are centralized refrigeration machines designed to produce chilled water (typically around 6.7°C or 44°F). This chilled water is then circulated by pumps through pipes to air handling units (AHUs) and fan coil units (FCUs) located throughout a building, which use the chilled water to cool and dehumidify the air.
Key components of a typical water-cooled chiller system include:
- Water-cooled Chillers: Generate chilled water using the refrigeration cycle (compressor, condenser, expansion valve, evaporator).
- Chilled Water Pumps: Circulate chilled water to AHUs/FCUs.
- Cooling Towers: Reject heat absorbed by the condenser water to the atmosphere, usually via evaporation.
- Condenser Water Pumps: Circulate condenser water between the chiller's condenser and the cooling tower.
- Make-up Water System: Replenishes water lost through evaporation in the cooling tower.
Piping for chilled water and condenser water systems typically consists of large-diameter carbon steel pipes, often insulated with materials like polyurethane (PU).
VRF Systems
VRF (Variable Refrigerant Flow) systems are direct expansion (DX) air conditioning systems that utilize variable-speed compressors and electronic expansion valves to modulate the flow of refrigerant to multiple indoor units based on demand.
Types include:
- Air-Cooled VRF: Rejects heat directly to the ambient air via outdoor condenser units with fans. More common due to potentially lower complexity and cost.
- Water-Cooled VRF: Rejects heat to a water loop, requiring cooling towers or other heat dissipation methods.
VRF systems connect one or more outdoor units to numerous indoor units (e.g., wall-mounted, ceiling cassette, ducted types) via a network of smaller-diameter copper refrigerant pipes using specialized branch joints (refnet joints). A single VRF outdoor unit can have a capacity up to ~16 RT, and multiple outdoor units (e.g., 3) can be modularly combined into a single system (~38 RT total), potentially serving up to 64 indoor units. VRF systems often employ proprietary centralized controllers, though integration with Building Management Systems (BMS) is also possible.
Technical Comparison Summary
Feature | Chiller System (Water-Cooled) | VRF System (Air-Cooled) |
---|---|---|
Overall System Complexity | Relatively simple concept, fewer major components | More complex distributed network at scale |
Space Requirement | Requires large central plant room(s) | Outdoor units can be distributed; requires pipe routing space |
Design Flexibility | Primarily determined by chiller sizes | High modularity and zoning flexibility |
Combined System Efficiency | Typically higher (e.g., ~0.83 kW/RT or better) | Generally lower than water-cooled chillers (e.g., ~0.95 kW/RT), efficient at part load |
Performance & Reliability | Consistent, well-understood | Highly dependent on installation quality |
Repairability / Maintenance | Fewer units, potentially specialized tasks | Numerous distributed components, potentially simpler individual repairs |
Installation Considerations
Piping: Chiller systems involve large-diameter (up to 300mm+) steel pipes requiring significant space and specialized welding. VRF systems use smaller copper refrigerant lines (e.g., up to ~16mm main lines), but extensive networks in large systems can also consume considerable space.
Equipment Handling: Chillers are heavy, requiring significant hoisting and rigging efforts and structural considerations. VRF outdoor units are modular and lighter, simplifying logistics.
Skills: Chiller installation typically requires pipefitters, welders, and engineers experienced with large hydronic systems. VRF installation requires technicians skilled in brazing copper refrigerant lines and understanding complex refrigerant management, though technicians familiar with split systems may adapt with specific VRF training. Installation quality (leak prevention) is critical for VRF reliability.
Project Management: Chiller delivery often represents a single major cost and schedule point. VRF allows for phased delivery and installation, potentially aligning better with progressive construction schedules, funding release, or renovation projects where minimizing disruption is key.
Maintenance Considerations
The maintenance approach differs significantly:
Chiller Systems: Involve fewer major pieces of equipment. Key tasks include regular cleaning of chiller tubes (evaporator/condenser), cooling tower maintenance (infills, water treatment), pump checks, valve inspections, and AHU/FCU filter/coil cleaning. While fewer items exist, tasks can be large-scale and may require specialized technicians or water treatment experts.
VRF Systems: Involve a much larger number of distributed components. Maintenance includes checking refrigerant pressure across many circuits, inspecting numerous outdoor units and compressors, checking potentially hundreds of expansion valves and indoor units, and addressing insulation integrity. While individual tasks might be simpler, the sheer quantity of components in a large system increases the number of potential failure points and the overall scope of routine checks and potential repairs. Fault finding in extensive refrigerant networks can be complex.
From a facility management perspective, large-scale VRF systems can present challenges in managing numerous distributed components and potential fault alarms compared to the centralized nature of chiller plants.
Conclusion
Both water-cooled chiller systems and air-cooled VRF systems are effective air conditioning technologies. The optimal choice depends on a detailed analysis of project-specific requirements:
- Chillers are often preferred for very large cooling loads (>1000 RT) where their superior efficiency at scale yields lower long-term operating costs, justifying the higher initial investment. Their centralized nature can simplify certain aspects of maintenance for large facilities.
- VRF systems excel in applications requiring granular zoning, design flexibility, phased installation, or where space for large central plants is limited (e.g., renovations, mid-size buildings). Their part-load efficiency is a significant advantage in varied occupancy scenarios.
Factors like first cost versus lifecycle cost, energy efficiency targets, building structure, installation logistics, maintenance capabilities, and required level of temperature control per zone must be carefully weighed.
This information provides a general comparison between chiller and VRF system types. Specific performance, cost, and application suitability will vary based on manufacturer, model, geographic location, and detailed project requirements.
For expert assessment, system design, equipment supply, and professional installation of Chiller or VRF systems, please contact ClimaPro.
ClimaPro
Email: [email protected]
We provide tailored climate control solutions to meet your building's unique needs.